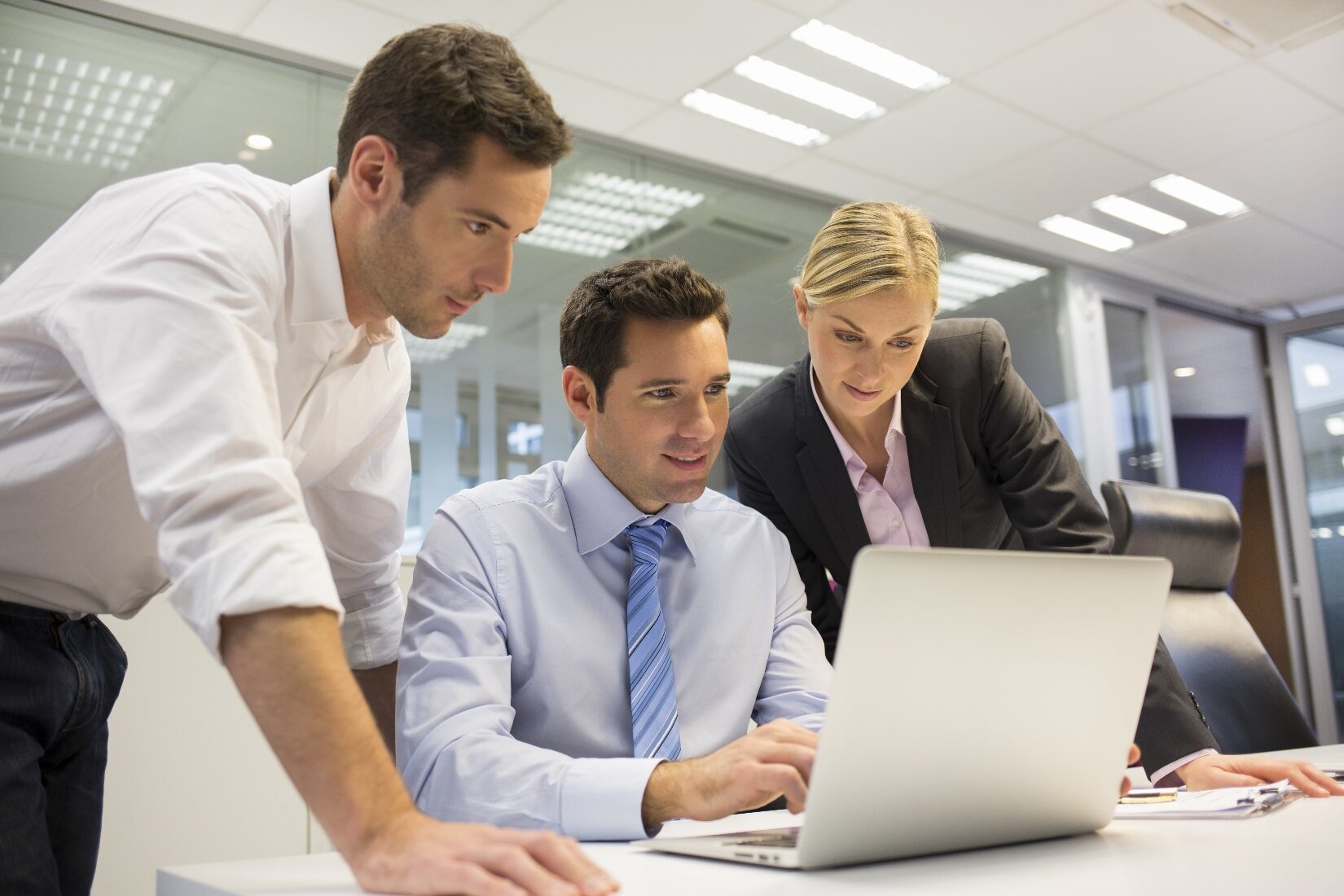
Feasibility and Concept Studies
As part of our end to end offering, Vecta has experience in developing studies to enable our customers to support their internal business cases. Some examples of sudies Vecta have completed include the following:
Investigation review and assessment of existing pipelines for a valued customer to determine the cost and construction methodology for the removal of existing expansion bellows and installation of new expansion loops. Vecta provided a feasibility study which included detailed cost estimate and construction methodology, preparation of the project schedule and a cost estimate.
Vecta were engaged to conduct a feasibility study for a new coal seam gas 80 TJ/d central processing plant in the Surat Basin Queensland. Part of this study would comprise a 20% cost estimate for the detailed design, procurement, construction and commissioning phases of project delivery. The total value of the project cost was $140M.
Our Client had a requirement for a Concept study of the installation of two re-purposed High Speed Disperser (HSD) machines in a re-allocated work area within their existing facility. Vecta were engaged to provide this Concept study. The scope included the following:
Review existing information to determine HSD layout options
Review existing power availability and requirements
Prepare preliminary layout sketches
Prepare a +/-30% Total Installed Cost Estimate ($500K TIC), including a Basis of Estimate document
Provide Concept study document
Vecta completed a project concept study and capital cost estimate for the consolidation of our customers manufacturing activities which would enable a significant increase to the production of water based paints. The new production facility was proposed to utilise new state of the art dispersion equipment and batch control processes. Some of the manufacturing and packaging equipment were to be relocated from another facility and rest were new. The batch control system was to be new integrated with the existing on-site system.
The intention of this new facility was to manufacture approximately 30 million litres of water based paint annually, based on a single 8 hours working shift, operating 5 days per week. In order to achieve this requirement, the facility would need to be highly automated, and recipe controlled, including some innovative time saving processes.
The P50 total installed cost was estimated to be $30 million at an accuracy of +/-25%.
Gas Development Project Concept Engineering
Selection and assessment of suitable gas treatment technology to upgrade the existing gas plant to accept fluid from the gas field,
process capacity checks of existing equipment,
development of HYSYS (dynamics) process models,
assessing environmental regulations and requirements for the disposal of gas containing H2S,
wastewater treatment,
review of existing flare / blowdown system and introduction of a staggered blowdown system