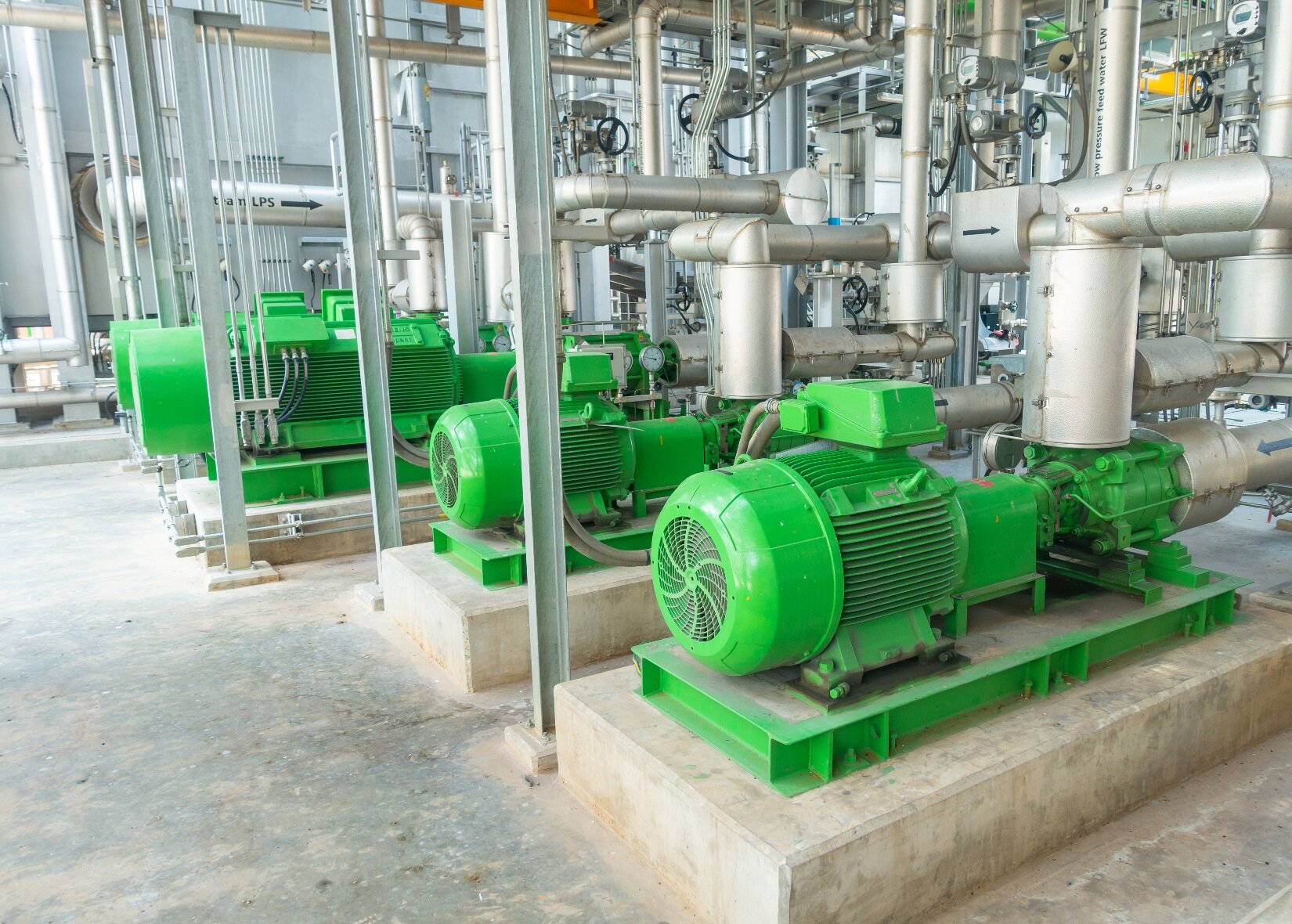
RAM Analysis
What is a RAM Analysis?
A RAM Analysis adds value to any facility whether it is a greenfield or brownfield site at virtually every stage of the asset lifecycle. It focuses on the availability of systems subjected to failure modes. By applying effective reliability techniques, informed decisions can be made regarding risk, efficiency, repair & maintenance during FEED phase of a new project or when addressing limitations of existing or expanding operations.
The results are used to determine in broad terms the overall maintenance philosophy and strategy for the asset, such as run-to-failure, condition monitoring, time-based preventive strategies and continuous monitoring.
Vecta can undertake either a complete facility RAM assessment focusing on all site systems or focus on specific systems which may be problematic in meeting current or future production demands.
Vecta takes a "bottom-up" approach for RAM modelling. This starts with looking at the taxonomy of assets and the system components and if available, reviews existing site data to determine the effects of individual component failure, often using a Reliability Block Diagram (RBD). If existing data does not exist or is incomplete, Vecta uses OREDA 2015 Handbook to determine suitable failure rates and times to repair.Vecta can provide 3D Laser Scanning services to capture plant as-built information for later use by project teams or clients as a record of what’s in the field.
What are the benefits of a RAM Analysis?
RAM modelling identifies areas of vulnerability which can affect operational availability and quantifies which assets and associated maintenance activities contribute most significantly to downtime. The system being modelled can then be optimized, including its configuration and level of redundancy.
Maintenance strategy can then be tailored to address any shortcomings in reliability of maintainable items. More specifically, the outcome of a RAM study can deliver tangible benefits including:
Reduced operation and maintenance costs whilst maintaining or increasing production levels
Identifying asset maintainable items, their failure modes, consequences and corrective actions
Identifying bottle necks and “production drivers”
Accurate forecasts of equipment lifecycle costs that reflect equipment age, duty cycle, and maintenance effectiveness.
A decrease in the duration of unplanned and planned outages
Alignment of maintenance resources based on the criticality of equipment to production revenue
Predicts the impact of equipment redundancy and sparing policy, and recommends suitable strategies to address any limitations
Undertakes “What-if” scenarios to validate reliability and availability targets.
The RAM process covers five essential steps
Reference Data gathering and structure
Review and RBD Validation
Modelling and Simulation
Validation and Documentation
Report generation
For the best outcome, Vecta encourages the involvement of key client stakeholders in the RAM process to ensure a high level of ownership of the outcome.
At Vecta, our RAM Consultants are experienced operational practitioners who have themselves been responsible for managing reliability, availability and maintainability to deliver business outcomes. They also understand the need to tailor a RAM process to suit the customer, each of whom have different needs. Our Consultants tailor the methodology to suit either greenfield or brownfield sites and can drill down to asset maintainable items as defined in OREDA Offshore and Onshore Reliability Data Handbook.
Vecta can undertake either a complete facility RAM assessment focusing on all site systems or focus on specific systems which may be problematic in meeting current or future production demands.